Increase Your Bottom Line With Efficient Warehouse Slotting
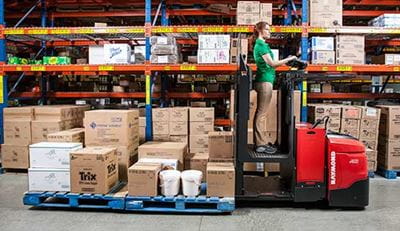
The costliest process in most warehouses is order picking. Picking requires a lot of labor, which can be expensive. If you want to save money in your warehouse or distribution center, a great place to start is by analyzing your slotting methods.
The costliest process in most warehouses is order picking. Picking requires a lot of labor, which can be expensive. If you want to save money in your warehouse or distribution center, a great place to start is by analyzing your slotting methods. If you can reduce the amount of labor required to pick a day’s orders, you’ve just increased your bottom line.
Before you start updating your slotting method, you first need to understand slotting and your slotting needs. The theory behind slotting is simple: Put the most-picked items in the most-reachable locations. Seems easy, right? However, data is crucial to this process. By analyzing the data, you can understand what you must store, how often stored items are accessed and the storage area you have available.
Slotting items is as easy as A, B, C
The first key to slotting is classification. To determine the classification of each item, you need to break them down into A, B and C categories based on how quickly the items move throughout the warehouse. Take a look at each of your SKUs and place them into one of three classifications:
- The SKUs with the greatest velocity, or movement, should be considered A items. In line with Pareto’s Law, these SKUs typically account for 80% of the picks and 20% of all inventory and are considered fast movers.
- Second are the B items. These typically account for 15% of the picks and 30% of total inventory.
- Lastly are C items, and although they only account for about 5% of all picks, they typically make up 50% of the inventory.
An ideal place to store your items
Typically, the most utilized shelving or racking areas are near the loading docks and are used for the fastest-moving items in the warehouse. This area is the best location for A items, either at the lowest pallet position or at the midlevel shelf. The B items are then located after A, assuming a return pick route is used, followed by the C items in the back. If using an S-pick route, consider the weight of each item. Heavier items should be at the bottom of the load so they should be picked first.
Maintenance also is a crucial part of the plan. When a new SKU comes in, make sure it doesn’t get hastily put away in the back of the warehouse. You need to categorize it into an A, B or C slot. Not sure where to start? There are tools that can help evaluate multiple data lines to select the perfect location for each item.
If space is a concern, consider a second-level order picker. These trucks offer the efficiency, simplicity and speed gained by picking to pallet jacks while allowing access to higher shelf levels, thus expanding available pick faces.
Warehouse slotting solutions
There are tools — such as a slotting program that fully integrates with AutoCAD to streamline warehouse workflow — that you can use to analyze the SKU size, weight and velocity, and determine the optimum storage location. Systems integrators offer tools like these to optimize your warehouse plans, capacity analysis, space and layout planning, equipment cost-benefit analysis, benchmarking and more.
If you are manually locating the items, simply list them in a spreadsheet based on picks per year in descending order (most to fewest). Both will help you plan the slotting process and offer greater net gains than manually locating items.
The process of warehouse slotting in its simplest form requires only a bit of research, a spreadsheet and a little extra work, but it can increase efficiencies and reduce travel time substantially — shrinking labor costs at the same time. If this feels overwhelming, don’t worry. There are tools and experts to help you re-evaluate your warehouse slotting strategy in support of developing an efficient and well-laid-out facility.
Submitted by: Jim Mihachik, Abel Womack, a Raymond Sales & Service Center
Plant Services, Today's Optimized Facility
Read the original post: https://www.plantservices.com/blogs/todays-optimized-facility/increase-your-bottom-line-with-efficient-warehouse-slotting/