Pick a winner: Focus your people by focusing on the right equipment
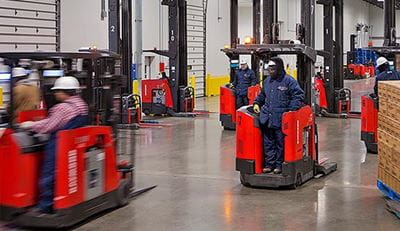
If you ask anyone outside the material handling industry to describe a lift truck, he or she will probably describe a classic counterbalanced lift truck: four wheels, a massive body behind a mast and forks, and a seat like a lawn tractor.
If you ask anyone outside the material handling industry to describe a lift truck, he or she will probably describe a classic counterbalanced lift truck: four wheels, a massive body behind a mast and forks, and a seat like a lawn tractor. These general-purpose lift trucks can perform a wide range of tasks, which accounts for their popularity with operations managers. Often, operations managers are focused on the need to move items but are not concerned with the details.
As production facilities are increasingly squeezed for maximum productivity and minimized operating costs — particularly labor — it makes sense for manufacturing and production facilities to consider the specialized equipment that warehousing and distribution centers have been using for decades. Think about the lifetime cost of operating a lift truck: Nearly 75 percent of the cost can be attributed to employing the operator. It makes fiscal sense to switch to specialized equipment that increases operator efficiency in specific tasks.
Here’s a quick rule of thumb: Check your lift truck utilization. Calculate the accumulated use hours (ending hours to starting hours) for a lift truck and divide that by the number of shifts in the period. If your total is four hours or less of lift truck use per period, your operator may have a significant amount of off-truck work to do — and climbing in and out of the seat may be hurting his or her overall productivity.
Choose a truck that will help the operator be most effective at the task at hand. If you are an operations manager at a manufacturing or production facility, consider applications where specialized equipment can boost productivity and save on labor costs:
- On docks or in work areas: If you need to only move pallets short distances and don’t require stacking or placement in racking, consider a walk-beside pallet truck. The operator likely needs to interact with the loads by completing paperwork that describes what the load is and its next destination. Adding walk-beside pallet trucks in work areas might mean more pieces of equipment, but it eliminates the labor time of driving back and forth between areas. It also can reduce the time work in process waits to move to the next area. If you do need to stack pallets in racking but require only a small dock area or manufacturing cell, a walk-beside stacker can fill the need at a low cost relative to a traditional ride-on lift truck.
- For long runs: If you need to get materials from one end of the plant to the other, consider a ride-on pallet truck (also called a walkie rider truck or pallet jack). Perhaps you need to get a pallet out of storage and delivered to the line. A narrow-aisle reach truck can do the pallet drop, and a pallet truck can run it out to the line. Allowing each truck to focus on what it does best not only improves efficiency but also allows operators to be more focused as well. Ride-on pallet trucks also work well for tractor-trailer loading and unloading, if there are no stacking requirements.
- For stockrooms: Inventory takes up footprint in the facility that cannot be used for production tasks. To minimize the amount of floor space absorbed by inventory, use a narrow-aisle truck, such as a reach, swing-reach or orderpicker truck. Because these lift trucks require less aisle space than traditional sit-down lift trucks, more room is available for value-add production activity.
- For multipurpose use: Even if you need to have one truck and operator perform many different tasks (the traditional stronghold for sit-down lift trucks), you may find that you maximize performance with a stand-up version. Operators use these trucks in a standing position, like a reach truck — but unlike a reach truck, there are no base legs that prevent the lift truck from traveling over dock plates. The stand up operating position may be preferred if the operators need to get off the forklift frequently, such as for checking paperwork, removing stretch wrap or fixing the parcel stack on the pallet.
Help the team at your manufacturing or production facility focus on the task by providing a truck that’s built for the job at hand. Equipment costs are typically dwarfed by labor costs, so invest in tools to save on labor.
Submitted on Thu, 05/21/2015 - 15:49
Plant Services, Today's Optimized Facility
Read the full post: http://www.plantservices.com/blogs/todays-optimized-facility/pick-a-winner-focus-your-people-by-focusing-on-the-right-equipment/